The ready mix concrete pump has revolutionized warehouse construction by enabling rapid placement of high-volume concrete slabs with precision and efficiency. Unlike traditional methods, this specialized concrete pump technology allows contractors to place thousands of cubic yards of concrete within tight schedules while maintaining strict flatness and levelness tolerances essential for warehouse operations. The strategic deployment of ready mix concrete pump systems transforms complex concrete placement challenges into streamlined processes, particularly for massive floor slabs, deep foundations, and high-bay structural elements that define modern logistics facilities.
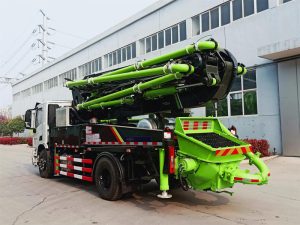
Pre-Construction Planning and Site Preparation
Successful implementation begins with meticulous planning before the concrete pump arrives on site. Surveyors must establish precise elevation benchmarks across the entire warehouse footprint, as even minor grading errors compound across large slabs. Coordinate with the ready mix concrete pump supplier to determine optimal positioning that maximizes boom reach while allowing continuous concrete truck access. For typical 100,000+ square foot warehouses, position the pump centrally to minimize pipeline drag distance and reduce labor for line repositioning. Prepare adequate curing compound and vapor barrier materials in advance since warehouse slabs often exceed placement capacities of 300 cubic yards per hour with a high-capacity ready mix concrete pump. Ensure sufficient access roads capable of supporting concrete mixer trucks and the concrete pump carrier, with particular attention to ground bearing capacity during rainy seasons when soil stability decreases.
Foundation and Floor Slab Applications
The ready mix concrete pump excels in constructing the critical concrete elements that define warehouse functionality. For deep strip foundations, the concrete pump delivers precise placement without trench cave-in risks by extending booms directly over excavation sites. When pouring monolithic slabs, the pump’s continuous operation prevents cold joints across expansive areas – a single high-output ready mix concrete pump can place 150-250 cubic yards per hour, completing typical warehouse floors in one continuous pour. Utilize laser screed systems in coordination with the concrete pump to achieve the FF/FL flatness specifications required for high-reach forklift operations. The pump’s adjustable discharge rate allows optimal concrete delivery speed matching the finishing crew’s pace, preventing premature setting in hot weather. For freezer warehouses, the ready mix concrete pump facilitates placement of insulated slabs with embedded heating elements, maintaining precise positioning during pumping operations.
Column and Structural Element Placement
Modern warehouse construction increasingly utilizes concrete columns and tilt-up panels for their durability and fire resistance. The ready mix concrete pump with articulated boom precisely places concrete into tall column forms up to 30 feet high without segregation, eliminating the need for cumbersome crane-and-bucket methods. When pumping to elevated sections, the concrete pump maintains constant pressure to ensure complete filling of complex formwork around steel reinforcement. For tilt-up panel production, position the ready mix concrete pump at the casting yard perimeter where its 360-degree rotation capability services multiple panels simultaneously. The boom’s precise control allows gentle concrete placement that prevents honeycombing in thin structural elements. During multi-story warehouse construction, the concrete pump progressively services higher floors by extending its boom through designated openings in the decking, significantly accelerating construction sequencing compared to traditional methods.
Efficiency Optimization Strategies
Maximizing the ready mix concrete pump productivity requires strategic operational planning. Schedule concrete delivery to maintain consistent flow – one mixer truck should arrive every 7-12 minutes to match the pump’s output capacity. Implement radio communication between pump operators, batch plant dispatchers, and mixer drivers to coordinate timing precisely. For large-scale warehouse projects, consider tandem pumping with two concrete pump units positioned at opposite ends of the slab to halve placement time. Optimize pipeline configuration using larger diameter lines (5-7 inches) for main runs and shorter flexible hoses at discharge points to reduce pressure loss. During extended pours, implement a relief operator schedule to maintain alertness with the ready mix concrete pump controls, as fatigue can compromise placement accuracy. Utilize the pump’s programmable pressure settings to automatically adjust for varying vertical heights when constructing multi-level distribution centers.
Quality Control and Testing Protocols
The concrete pump introduces unique quality considerations during warehouse construction. Monitor concrete consistency continuously using slump tests at the pump hopper – maintain 4-6 inch slump for optimal pumpability without segregation. Implement temperature control measures when pumping in extreme conditions: use chilled water in hot climates and heated enclosures for cold-weather pouring to prevent setting time variations. For reinforced slabs, coordinate with steel inspectors to verify clearance before pumping begins since the ready mix concrete pump’s rapid placement leaves minimal correction time. Embed vibration monitoring sensors in deep footings to confirm complete consolidation during pumping operations. Collect test cylinders at the concrete pump discharge point rather than from mixer trucks to account for potential material modification during pumping. Document pumping pressure and line cleaning procedures to validate compliance with project specifications for critical structural elements.
Safety Implementation for Warehouse Sites
Operating a ready mix concrete pump on congested warehouse sites demands rigorous safety protocols. Establish a 360-degree exclusion zone around the concrete pump during operation, clearly marked with barrier tape. Implement spotter communication systems using standardized hand signals when the operator’s visibility is obstructed. For boom pumps extending near power lines, enforce minimum 10-foot clearance distances with proximity alarms. Secure all pipeline connections with dual locking mechanisms before pressurization to prevent blowouts during high-pressure pumping. Conduct daily inspection of the concrete pump’s structural components, focusing on boom hinge points and outrigger pads that bear significant loads on potentially unstable ground. Provide comprehensive training for pump operators on emergency shutdown procedures specific to warehouse environments where multiple trades work simultaneously.
Maintenance and Troubleshooting
Maintaining peak ready mix concrete pump performance during extended warehouse projects requires disciplined maintenance routines. Flush pumping lines with 20 gallons of water after every 50 cubic yards to prevent buildup that constricts flow. Monitor hydraulic fluid temperature continuously – sustained operation above 180°F accelerates component wear. Implement a greasing schedule every 200 operating hours for boom joints and every 50 hours for pumping cylinder pivot points. Carry critical spares including pipeline gaskets, hydraulic hoses, and filter elements to minimize downtime. When troubleshooting common concrete pump issues:
For pipeline blockages, reverse pump direction briefly before attempting forward flushing
If pressure fluctuates abnormally, inspect wear plates and grinding rings immediately
When boom movement hesitates, check hydraulic fluid levels and filter condition
Maintain detailed maintenance logs to identify patterns that might indicate developing component failures before they interrupt construction schedules.
Cost Management and ROI Analysis
The economic justification for ready mix concrete pump deployment in warehouse construction reveals compelling advantages. Though rental costs range $1,500-$3,500 daily, the productivity gains typically deliver 3:1 return on investment by reducing placement time by 60-70% compared to manual methods. Labor savings prove substantial – a single concrete pump replaces 15-20 workers with wheelbarrows while achieving better consistency. Calculate fuel consumption at 4-8 gallons per hour depending on pump size and workload intensity. For long-duration projects, negotiate weekly or monthly rental rates for the concrete pump that reduce daily costs by 25-40%. The elimination of construction joints through continuous pumping minimizes future maintenance expenses for warehouse floors – a critical factor in facilities using high-reach forklifts where joint deterioration causes operational hazards and costly repairs.
By integrating ready mix concrete pump technology into warehouse construction planning and execution, contractors achieve unprecedented efficiency while meeting the demanding specifications of modern logistics facilities. The pump’s ability to place vast concrete volumes with precision accelerates project timelines significantly, often turning months of work into weeks. Properly implemented, this technology transforms concrete placement from a construction bottleneck into a strategic advantage, ensuring warehouses meet their operational readiness deadlines while maintaining the structural integrity required for decades of heavy industrial use. The combination of speed, precision, and cost efficiency makes the concrete pump an indispensable asset in contemporary warehouse development, setting new standards for what’s achievable in industrial construction.
Leave a Reply