In the modern construction industry, speed and efficiency are essential, especially in standardized building projects where tight deadlines and uniform quality requirements dominate the workflow. The trailer concrete pump has emerged as a key tool for achieving fast and efficient concrete pouring on such construction sites. Known for its flexibility, high-pressure output, and mobility, this type of pump is widely used for rapid concrete delivery in various structural applications. For contractors aiming to optimize the speed of standardized building rapid pouring, understanding the factors that influence the performance of trailer concrete pumps is crucial. In particular, those using a small concrete pump in confined or smaller-scale projects must pay close attention to specific operational and technical considerations to maintain efficiency and quality.
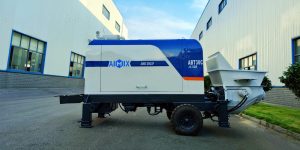
The Role of Trailer Concrete Pump in Standardized Building Projects
A trailer concrete pump is a concrete conveying device mounted on a trailer, powered by a diesel or electric engine, and capable of transporting concrete through pipelines to high or distant locations. It is especially advantageous in standardized building projects where repetitive structures—like prefabricated units, apartment blocks, or public housing—demand a consistent pouring method across similar modules or floors. The ability to pump concrete continuously and precisely helps eliminate delays and reduce manual labor, contributing directly to faster completion times.
However, achieving maximum speed in pouring depends on more than just having the right machine. Several interconnected factors impact how quickly a trailer concrete pump can deliver and pour concrete effectively on standardized building sites.
Concrete Mix Quality and Pumpability
One of the most critical factors influencing the speed of pouring is the quality and composition of the concrete mix. Whether using a trailer concrete pump or a small concrete pump, the mix must have the right balance of water, cement, sand, and aggregates to ensure smooth pumping through long or narrow pipelines.
For standardized building projects, the concrete mixture should have sufficient workability (typically a slump of 150–180mm) to flow easily without causing blockages. If the concrete is too dry or contains oversized aggregates, it may lead to pump failures or pipe clogs, significantly reducing the pouring speed. Conversely, a mix with too much water can lead to segregation and lower structural strength, defeating the purpose of quality construction.
Superplasticizers or water-reducing agents are often added to enhance pumpability without compromising strength. Ensuring consistent batching and avoiding overmixing are also important to maintain flow efficiency, especially when working with small concrete pumps that may be more sensitive to mix irregularities.
Pump Output Capacity and Machine Condition
The capacity and technical condition of the trailer concrete pump are vital to determine how much concrete can be pumped per hour. Most standard trailer pumps can deliver between 30 to 80 cubic meters per hour depending on the model and configuration. However, this theoretical capacity can only be achieved if the pump is well-maintained and properly operated.
Older or poorly serviced pumps may suffer from reduced output due to wear in the pumping cylinders, valves, or seals. Similarly, insufficient lubrication or hydraulic issues can slow down the stroke speed, decreasing productivity. Using a small concrete pump on a job that demands high volume can also result in bottlenecks, causing unnecessary delays.
To ensure optimal pouring speed, regular maintenance, timely replacement of wear parts, and pre-operation checks are essential. Choosing a pump with an appropriate output rating for the project’s scale also ensures that productivity targets are consistently met.
Pipeline Layout and Configuration
The efficiency of concrete pumping is heavily influenced by the layout and setup of the delivery pipeline. For high-speed pouring, the pipeline should be designed to minimize bends, vertical rises, and friction. Each bend or elevation adds resistance, which reduces the pumping speed and may strain the trailer concrete pump.
Use steel pipes for long-distance or high-pressure pumping, and make sure all joints are tightly sealed to prevent leakage. For smaller projects or confined workspaces, a small concrete pump with a flexible hose may be preferable, but it’s important to keep the line as short and straight as possible.
Additionally, priming the pipeline before pouring is a critical step. A proper priming mix (often a mortar or slurry) helps reduce friction and prevent initial blockages that can slow down operations right from the start.
Site Readiness and Coordination
The readiness of the construction site and the coordination between teams play a major role in the speed of pouring operations. A trailer concrete pump can only be efficient if it is supported by well-organized logistics. This includes having formwork ready, reinforcement installed, and labor teams prepared to manage the poured concrete.
In standardized buildings, repeating the same construction cycle (e.g., floor-by-floor or unit-by-unit) requires seamless scheduling between concrete batching, pump arrival, and on-site placement. Any delay in one area—such as unprepared formwork or a missing labor crew—can cause the trailer pump to sit idle, wasting valuable time and energy.
Clear communication between the pump operator, batching plant, and on-site supervisor ensures smooth transitions and helps avoid downtime. For small concrete pumps, which are often used in modular or prefabricated projects, precise timing and coordination are even more crucial due to their limited output capacity.
Environmental and Weather Conditions
External conditions like temperature, humidity, and wind can affect both the concrete itself and the pumping operation. On hot days, concrete can start setting more quickly, increasing the risk of blockages and requiring faster pouring. On cold or rainy days, the mix may become less workable, requiring adjustments to the pumping process.
Trailer concrete pumps operating in extreme conditions must be monitored closely. Operators may need to adjust pumping pressure, use additives to modify setting times, or shelter pipelines to maintain flow. Small concrete pumps, being less powerful, may be more susceptible to delays caused by temperature or moisture changes, requiring careful mix adjustments and on-site adaptations.
Operator Skill and Experience
Even with top-quality trailer concrete pump equipment and a perfect concrete mix, the skill of the pump operator ultimately determines how smoothly and quickly concrete is poured. Experienced operators know how to manage pressure levels, detect early signs of pipeline blockage, and maintain a steady flow without surges or air pockets.
For small concrete pump users, operator expertise is even more important because the margin for error is smaller. Precision in pipeline handling, timing, and pump speed adjustments is key to maximizing productivity and avoiding waste or damage.
In conclusion, the speed of standardized building rapid pouring using a trailer concrete pump is influenced by a variety of technical, logistical, and environmental factors. From choosing the right concrete mix and ensuring proper equipment maintenance to managing pipeline setup and site coordination, every detail plays a part in achieving high productivity. Contractors working with small concrete pumps must be especially mindful of operational limits and site conditions to maintain consistent output. With a clear understanding of these factors and a commitment to best practices, construction teams can significantly improve pouring speed and project efficiency in standardized building projects.
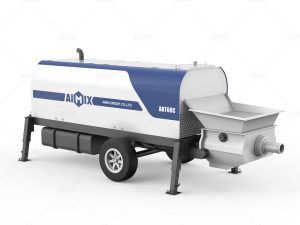
Leave a Reply