When pouring precast concrete plates for a five-layer office building, understanding and calculating the cost of concrete pump—especially a portable concrete pump—is critical for both budgeting and project efficiency. Portable pumps are widely favored in commercial and mid-rise construction due to their mobility, compact design, and strong pumping capacity. However, to ensure accurate cost planning, contractors and project planners need to consider multiple factors beyond the price tag of the pump itself.
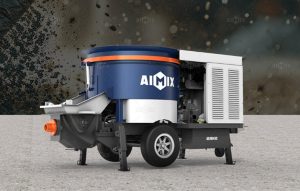
Understanding the Basics of Portable Concrete Pump Costs
The portable concrete pump is ideal for pouring tasks in buildings with multiple levels, especially when the structure involves repeated concrete pouring like precast floor plates. These machines combine high-pressure delivery, ease of movement on-site, and compatibility with different types of concrete mixes. However, the cost of using one extends beyond the initial purchase or rental price.
To calculate the cost of concrete pump for a project involving five layers of precast concrete plates, one must take into account several direct and indirect elements: acquisition or rental costs, transport, labor, fuel or electricity, maintenance, and concrete delivery volumes.
Acquisition vs. Rental: Choosing the Right Strategy
The first major consideration is whether to buy or rent the portable pump. For contractors who frequently undertake similar multi-level projects, purchasing may be more cost-effective in the long run. The price of a portable concrete pump varies based on its output capacity (measured in cubic meters per hour), power type (diesel or electric), and brand reputation.
For example:
- A diesel-powered portable concrete pump with 30–40 m³/h output might cost between $18,000 to $25,000.
- An electric version with similar capacity could range from $15,000 to $22,000, depending on motor size and features.
However, if your use is occasional or limited to this single five-story office project, renting may be more economical. Daily rental prices can range from $200 to $400, depending on your location, availability, and included services (such as operator and fuel).
Assuming you need the equipment for around 15 working days to complete the full pour cycle for five floors, the estimated rental cost would be:
- 15 days × $300/day = $4,500
Estimating Fuel or Energy Costs
For diesel portable concrete pumps, fuel consumption is a major operating cost. A typical small-to-medium diesel pump might consume 5–8 liters of diesel per hour. If each floor’s precast concrete plate pouring takes around 6 hours, and you’re pouring 5 floors, you’d be looking at:
- Total pump time: 5 floors × 6 hours = 30 hours
- Average diesel use: 6 L/h × 30 hours = 180 liters
- If diesel is priced at $1.20/L, fuel cost = 180 × $1.20 = $216
In contrast, electric pumps draw 15–30 kW per hour depending on load. If your site has stable power, the cost may be lower:
- Total kWh: 25 kW × 30 hours = 750 kWh
- At $0.12 per kWh, total energy cost = 750 × 0.12 = $90
Thus, energy costs can differ by over 50% depending on your chosen power source.
Labor and Operator Fees
Most portable concrete pumps require at least one trained operator, along with assistants to manage hoses and coordinate the pouring. Daily labor fees will vary based on region, but you can estimate:
- Operator wage: $120/day × 15 days = $1,800
- Two assistants: $80/day × 2 × 15 days = $2,400
- Total labor: $4,200
It is crucial to include these labor costs when calculating the overall cost of the concrete pump’s role in your project.
Concrete Volume and Pumping Time
Let’s assume each precast concrete plate (per floor) requires 20 m³ of concrete, and there are five floors:
- Total concrete: 5 × 20 m³ = 100 m³
A portable pump with 30 m³/h output will complete one floor’s pour in less than a day. However, time also includes setup, alignment, cleaning, and repositioning. Therefore, you must calculate not only the raw pumping hours but the full operational cycle per pour.
- Estimated cost impact of time inefficiencies = +15%
- Adjusted total hours = 30 hours × 1.15 = 34.5 hours
This factor is important because fuel, energy, and labor costs will all increase proportionally with time.
Maintenance and Wear-and-Tear
Even on short-term projects, pump maintenance (cleaning, hose checks, and grease refills) is essential to avoid delays or malfunctions. Maintenance cost might include:
- Lubricants, tools, cleaning agents: $100–$200/project
- Emergency part replacement (e.g., hose, seals): $200–$400
- Total estimate: $300–$600
For rental units, some of these costs might be absorbed by the rental company, but you should confirm this in the contract.
Transport and Setup
Don’t overlook transport. Moving a portable concrete pump to and from your office building site can cost between $100 to $500 depending on the distance and equipment size. Setup services (leveling, anchoring, test run) might cost extra if outsourced:
- Total logistics: $300–$700
Total Cost Estimate Breakdown
Now let’s put it all together:
Cost Component | Estimated Cost (USD) |
---|---|
Rental (15 days) | $4,500 |
Fuel (diesel model) | $216 |
Labor (Operator + Assistants) | $4,200 |
Maintenance & Wear | $400 |
Transport & Setup | $500 |
Total | $9,816 |
For electric pumps, you could reduce the fuel/energy and possibly the maintenance slightly:
- Substitute diesel fuel with $90 electric power
- Slightly lower wear-and-tear estimate: $300
- Adjusted Total: ~$9,474
This breakdown helps you understand how much the cost of concrete pump operation can amount to when pouring for five floors of precast plates in an office project.
Final Thoughts: Plan Wisely for Pumping Success
The portable concrete pump is a powerful tool that streamlines the entire precast plate pouring process. However, its effective use demands a clear understanding of operational costs across labor, energy, logistics, and maintenance. When planning your office building project, make sure to conduct a full breakdown of these variables. This will not only prevent budget overruns but also ensure your concrete pouring process remains smooth and consistent across all five floors.
By using the above methodology, contractors and site engineers in both developing and developed regions can better forecast expenses and keep the construction project within financial control.

Leave a Reply