When searching for mini concrete pumps for sale, buyers often focus on performance metrics like output capacity and pressure while overlooking a critical operational challenge: excessive vibration when the pump is stationary during transportation. This shaking phenomenon, common in both mini concrete pumps and larger concrete pump stationary models, can lead to premature wear of components, safety hazards, and reduced operational efficiency. The vibrations originate from multiple sources including engine imbalance, hydraulic pulsation, improper mounting, and structural resonance, all of which become magnified when the pump isn’t properly stabilized during transit between job sites.
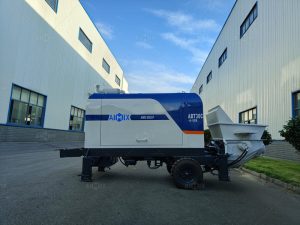
This comprehensive guide examines the root causes of stationary shake in mini concrete pumps during transportation and presents practical solutions to mitigate these vibrations. We’ll explore mechanical adjustments, proper mounting techniques, hydraulic system optimizations, chassis stabilization methods, and operational best practices. By implementing these strategies, operators can significantly reduce equipment vibration, extend the pump’s service life, improve safety, and maintain consistent concrete placement quality. Whether you’re evaluating mini concrete pumps for sale or troubleshooting an existing concrete pump stationary unit, understanding these vibration control techniques will help you maximize your equipment’s performance and longevity.
Understanding the Causes of Stationary Shake in Mini Concrete Pumps
Before addressing solutions, it’s crucial to understand why mini concrete pumps experience such pronounced vibrations when stationary during transportation. The shaking stems from three primary sources: mechanical forces generated by the pump’s operation, structural characteristics of the pump itself, and external factors related to transportation conditions. The diesel or electric engine produces inherent vibrations that transfer through the frame, while the reciprocating motion of the concrete pumping mechanism creates rhythmic pulses. These vibrations become particularly problematic when the pump is stationary because unlike mobile operation where movement dissipates some energy, stationary operation allows vibrations to accumulate and amplify through the structure.
Hydraulic systems in mini concrete pumps for sale contribute significantly to the vibration profile. Pressure fluctuations in the hydraulic circuits, especially during the switching between pumping cycles, create sharp impulses that translate into whole-machine shaking. The compact size of mini pumps actually exacerbates this issue compared to larger concrete pump stationary units, as there’s less mass to absorb and dampen the vibrations. Additionally, the natural frequency of the pump’s frame and mounting system may coincidentally match the operational vibration frequency, creating a resonance effect that dramatically increases shaking amplitude. Transportation adds another layer of complexity, as road-induced vibrations interact with the pump’s operational vibrations, potentially creating harmonic amplification during transit.
Mechanical Solutions to Reduce Pump Vibration
Addressing vibration at its mechanical sources provides the most effective reduction in stationary shake for mini concrete pumps. The first critical area is engine mounting and isolation. Modern mini concrete pumps for sale should incorporate high-quality vibration isolation mounts between the engine and main frame. These specialized mounts, typically made from compounded rubber or hydraulic damping materials, absorb and dissipate engine vibrations before they can transfer to the rest of the machine. For older pumps or those showing excessive vibration, upgrading to advanced anti-vibration mounts can yield immediate improvements. The mounting system should be inspected regularly as worn or compressed mounts lose their damping effectiveness.
The concrete pumping mechanism itself requires careful balancing. The piston assembly, swivel joints, and distribution valve in mini concrete pumps must be precision-aligned to minimize unbalanced forces. Worn wear plates or misaligned components create additional vibration sources that compound during operation. Implementing a rigorous maintenance schedule that includes checking and adjusting these components can prevent vibration issues from developing over time. Some high-end concrete pump stationary models incorporate counterbalance systems that actively offset the pumping mechanism’s vibrations, though this technology is less common in mini pumps due to size constraints. However, aftermarket dynamic balancers can sometimes be fitted to particularly problematic units.
Hydraulic System Adjustments for Smoother Operation
The hydraulic system in mini concrete pumps for sale plays a dual role in both generating and potentially mitigating vibrations. Pressure pulsations within the hydraulic circuits are a major contributor to overall machine vibration. Several strategies can smooth out these pulsations and reduce consequent shaking. First, ensuring proper hydraulic fluid levels and quality is essential – contaminated or aerated fluid transmits vibrations more readily. Installing pulsation dampeners or accumulators in the hydraulic lines can significantly smooth out pressure spikes, though space limitations in mini pumps may require compact, specially designed dampeners.
The hydraulic control parameters also affect vibration characteristics. Many modern mini concrete pumps feature adjustable pump stroke rates and pressure ramp controls. Optimizing these settings can find a sweet spot between pumping efficiency and vibration generation. Slower, more controlled movement of hydraulic actuators generally produces less vibration than rapid, jerky motions, though this must be balanced against concrete placement requirements. Some advanced concrete pump stationary units employ predictive valve timing algorithms that anticipate and compensate for vibration-causing pressure transitions, technology that is gradually trickling down to mini pump designs.
Structural Reinforcement and Chassis Modifications
The physical structure of the mini concrete pump itself significantly influences how vibrations manifest during stationary operation. The frame design and material composition determine its natural resonant frequencies and vibration damping characteristics. While buyers evaluating mini concrete pumps for sale can’t typically modify the fundamental frame design, several aftermarket solutions can enhance structural vibration resistance. Adding strategically placed stiffening plates or gussets to high-stress areas can alter the frame’s resonant frequencies away from operational vibration ranges. This must be done carefully to avoid creating new stress concentrations.
The mounting system between the pump unit and transport chassis deserves particular attention. Many vibration issues stem from inadequate or improperly installed mounting hardware. The interface between pump and chassis should use vibration-isolating materials and proper torque specifications. For pumps regularly transported on trailers, considering the trailer’s own vibration characteristics is important – a stiff, high-quality trailer frame will transmit fewer road vibrations to the pump than a flexible, lightweight frame. Some operators install secondary vibration isolation systems between the pump and trailer for additional damping.
Transportation-Specific Vibration Control Measures
When moving mini concrete pumps between job sites, special precautions can prevent vibration-related issues. Proper securing of the pump for transport is paramount – loose mounting allows micro-movements that can develop into significant shaking during road travel. All locking pins and tie-downs should be verified before each move. The transport speed should be moderated, as higher speeds generate more vibration energy that can loosen components or fatigue materials. Route selection also matters – smooth highways produce less vibrational stress than rough back roads.
During actual pumping operations when stationary, the setup location significantly affects vibration transmission. Placing the mini concrete pump on stable, level ground is essential. When possible, positioning the pump on concrete pads or steel plates provides a more stable base than bare earth. Outriggers should be fully extended and properly loaded to maximize stability. Some operators use additional vibration-absorbing mats under the outrigger feet for sensitive applications. The pump’s orientation relative to the work area can also matter – aligning the pumping axis with the stiffest chassis direction often reduces visible shaking.
Operational Techniques to Minimize Vibration Effects
Even with optimal equipment, operator technique influences vibration levels in mini concrete pumps. Smooth, consistent operation generally produces less vibration than erratic, stop-start pumping. Maintaining steady engine RPMs rather than constantly varying speed helps avoid exciting different vibration modes. The concrete mix design itself affects vibration – properly proportioned mixes with adequate workability flow more smoothly through the system, reducing pulsations. Operators should avoid running the pump dry or with partial loads, as these conditions often increase vibration.
Regular monitoring of vibration levels can help identify developing issues before they become severe. Some mini concrete pumps for sale now include basic vibration sensors, while aftermarket monitoring systems can be added to older units. Establishing baseline vibration signatures during normal operation allows comparison over time – increasing vibration levels often warn of developing mechanical issues like worn bearings or misalignments. This predictive maintenance approach can prevent minor vibration issues from escalating into major problems.
Innovative Technologies in Vibration Reduction
The latest generations of mini concrete pumps for sale incorporate several innovative technologies to address stationary vibration issues. Active vibration cancellation systems, adapted from aerospace applications, use sensors and counteracting actuators to neutralize vibrations in real time. While still relatively rare in mini pumps due to cost and complexity, these systems represent the future of vibration control. More commonly available are improved materials like composite damping layers built into pump structures and advanced elastomeric compounds for vibration isolation mounts.
Some manufacturers now offer concrete pump stationary models with tunable vibration characteristics, allowing operators to adjust damping parameters for specific job requirements. Variable-frequency drive systems for electric pumps provide smoother power delivery than traditional fixed-speed designs. Hydraulic system innovations include more sophisticated accumulators and pressure smoothing valves that reduce pulsations at their source. As these technologies mature and production scales increase, they’re becoming available in smaller, more affordable mini concrete pump models.
Long-Term Maintenance for Sustained Vibration Control
Maintaining low vibration levels in mini concrete pumps requires an ongoing commitment to proper maintenance. All vibration-sensitive components should be included in regular service intervals. Mounting hardware should be inspected for proper torque and condition – loose bolts are a common source of increasing vibration over time. Hydraulic hoses and connections need regular checking, as leaks or degraded hoses can alter system dynamics. Structural welds and frame components should be examined for cracks that might change vibration characteristics.
Lubrication plays a crucial role in vibration control. Properly lubricated moving parts operate more smoothly with less vibration generation. The lubrication schedule should account for operating conditions – pumps used in dusty environments or extreme temperatures may need more frequent servicing. Keeping detailed maintenance records helps identify vibration-related trends and schedule preventive interventions before problems escalate.
Achieving Smooth Operation in Mini Concrete Pumps
Reducing stationary shake in mini concrete pumps during transportation requires a multifaceted approach addressing mechanical, hydraulic, structural, and operational factors. By systematically evaluating and optimizing each of these areas, operators can significantly decrease vibration-related issues, extending equipment life and improving job site safety and efficiency. When evaluating mini concrete pumps for sale, buyers should consider vibration control features alongside traditional performance metrics, as these directly impact long-term operating costs and reliability.
The solutions presented here range from simple adjustments to more involved modifications, allowing operators to select approaches matching their specific needs and resources. Even implementing a subset of these recommendations can yield noticeable improvements in vibration reduction. For existing concrete pump stationary units showing excessive vibration, a step-by-step troubleshooting approach identifying the dominant vibration sources will provide the most cost-effective improvements. With proper attention to vibration management, mini concrete pumps can deliver their full potential of portable, efficient concrete placement without the drawbacks of excessive shaking during transportation and operation.
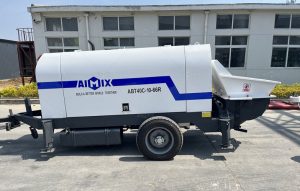